The learning capability of a food organization
This article is about the learning capability of a food organization regarding food safety. In food safety management, it is important to identify emerging risks in time and to anticipate them. When a company demonstrably manages food safety risks, this has a positive impact on confidence in the company and the related performance. How do you set up a learning organization with regard to food safety? First of all, what is involved in managing food safety?
5 main actors
From a helicopter view of food safety management, there are five main actors.
• the food company
• the company’s customers and consumers
• the company’s suppliers
• the Food legislation
• the Food quality standards
Food safety learning: Stakeholders
Within the food company there are different departments and roles regarding food safety. The management determines the company’s objectives and allocates the investments. It is important that management invests in the right food safety structure and systems that enable the company to perform well: business performance management (BPM).
Food safety learning: Costumers
The customers depend on the company’s food safety performance. The company must properly align its activities with the requirements and wishes of customers and consumers regarding the products and services provided, like allergen or origin information: demand relationship management (DRM).
Food safety learning: suppliers
The suppliers have the greatest impact on the company’s food safety performance. Most recalls are also caused by the suppliers of food companies. As a food company, you have the best grip on your own performance, because you can manage and monitor it yourself. The supplier must properly attune its activities to the requirements and wishes of the food company with regard to the products and services supplied: supply relationship management (SRM).
Food safety learning: Legislation
As a food company, you have to take into account all facets of food legislation. For example, the legislation in the EU is designed in such a way that as a food company you are responsible for food safety yourself. Legislation has a major impact on the framework in which a food company can operate. It is therefore important to make managing these legislative issues part of business operations: legislation management (LM).
Food safety learning: Quality standards
As a food company, you have to take the food quality standards into account. Both business to business customers and retailers often require a supplier to be certified to a standard recognized by the Global Food Safety Initiative (GFSI): BRC Food, IFS Food, FSSC22000 or SQF. It is therefore important to make managing this certification part of the business: certification management (CM).
When you combine the 5 main actors regarding Food Safety management with the 4 main themes that the QA department normally works on, you get the following definition:
Food safety learning Food Safety Compliance management:
Management of business performance, demand and supply relations, legislation and certification with regard to food safety, taking into specifications, quality activities, traceability and assessment.
You can try to carry out these management activities from a systems thinking perspective. Depending on the importance of the activity, you can organize it at different levels.

Level of activity organization
- Activity: the activity is performed without pre-structured recording and/or tuning of the input or output of the activity.
- Process: the activity is performed with structured recording of the input or output of the activity between 2 actors.
- Systematic: the activity is performed with structured recording of the input or output of the activity and control between 2 actors.
- Chain: a set of predefined activities between multiple actors are performed with structured recording of the input or output of the activities and control thereof.
- Holistic: a set of predefined activities between multiple actors are performed with structured recording of the input or output of the activities and control thereof, also taking into account the signaling of external influences (triggers) that can lead to new ones necessary tasks and activities.
Connectivity phases
The way in which the activities are carried out within the company provide an indication of the connectivity in the organization. In an organization with a good infrastructure and predefined processes and systems, business-critical activities will be organized at least at the system level, allowing the Deming circle (Plan-Do-Check-Act) to take place.
Phases of Connectivity:
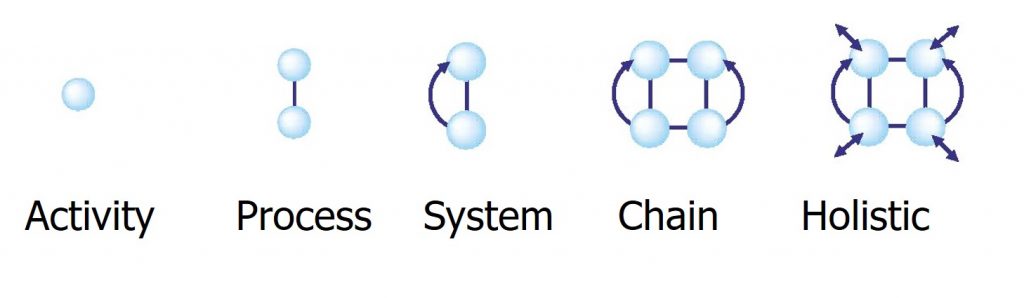
Intra-connected
The company is set up for the activity and process connectivity phases. An activity takes place within the company, whereby coordination takes place about the input and/or output of this activity.
Inter-connected
The company is set up for the system and chain connectivity phases. An activity takes place within the company and with directly involved actors in the chain (relations: suppliers and customers), whereby coordination takes place about the input and/or output of this activity and a predefined check is performed on the input and output and feedback is given on the outcome of the activity
Extra-connected
The company is holistically organized. An activity takes place within the company, in the chain and with (in)directly involved actors on the output of the company (such as inspection bodies such as the Food Safety Authority and certifying parties), whereby coordination takes place about the input and/or output of this activity and a predefined check is performed on the input and output and feedback is given on the outcome of the activity.
The connectivity phases of a company are directly related to the learning capacity of the organization. An intra-connected organization is more inwardly oriented than an inter or extra-connected organization. As a result, such a company will be less able to identify emerging food safety risks or legislation in time that must be proactively anticipated. These three organizational forms are explained in more detail below.
Intra-connected organization
The company is internally focused. Within the food company, cooperation is based on input and output. There is little coordination between departments. Questions from customers and consumers are handled on an ad hoc and reactive basis. This also applies to complaints against the company’s suppliers. There is no overview of the latest Food legislation and unannounced audits are not achieved because not all certification requirements are continuously met. The company knows that something has happened with a food safety theme or knows that something is happening. In the Netherlands, for example, stricter rules regarding Listeria Monocytogenes control have been in place since the end of 2018. There have been companies that have not anticipated this in time, as a result of which, for example, the best before date of the produced meals had to be reduced from 10 to 4 days. This had major consequences for the supply chain. As a result, a smoked salmon producer was no longer able to export and saw its turnover halve as a result.
Inter-connected organization
The company works in a systematic manner and is chain-oriented. Within the food company, cooperation is based on the Deming circle (Plan-Do-Check-Act). There is good coordination between departments. Inquiries from customers and consumers are handled routinely and proactively. This also applies to complaints against the company’s suppliers. There is an overview of the latest food legislation and this is known throughout the company and unannounced audits are no problem because all certification requirements are continuously met. The company knows that something is happening with a food safety theme or even knows why something is happening. For example, after a visit from the Food Safety Authority, a company knows that work needs to be done on shelf life studies for Listeria Monocytogenes and starts working on this, with log 2 as the maximum outgrowth value. On a subsequent visit by the Food Safety Authority, all shelf life of the products will be reset to a maximum of 4 days best before date, because the Food Safety Authority has in the meantime adjusted the requirements in their guidelines (In the Netherlands Infosheet 85) to a maximum of 0.5 log growth. A large producer of meat products was closed as a result.
Extra-connected organization
The company works completely integrated and is holistically designed as a real learning organization. Within the company, everyone knows their role and is part of the sense and respond function regarding the identification of opportunities and risks that could have an impact on the company from the world. The company knows why something is happening with a Food Safety theme or even knows that something is going to happen. The Food Safety Authority in the Netherlands publishes in Infosheet 85 the desired method with which Listeria Monocytogenes must be controlled. This information sheet is updated annually with new requirements regarding control. Food companies must therefore organize themselves in such a way that they are aware of changes in this Infosheet, so that they continue to comply. This also applies to other themes, such as the control of ethylene oxide in sesame seeds.
Food Safety Compliance: learning capability stages
These stages of connectivity can be used to characterize the learning capability of the organization in the field of Food Safety Compliance.
- Getting Connected: food safety management is process-driven, everyone works according to instructions that apply to the department.
- Networking: food safety management is systematically managed and attention is also paid to chain assurance, whereby we work according to cross-departmental routines and agreements.
- Sense and Respond: food safety management is designed holistically with regard to the external risks that can impact the company’s total performance.

Food Safety Compliance: certification management (CM)
Getting Connected | Networking | Sense and Respond |
the quality system is set up in accordance with the standards, but is not aware of new doctrines. A month before the audit, all sails are pulled (Dutch expression for doing your best), an unannounced audit is not a good idea. | the quality system is set up in accordance with the standards and the latest guidelines. Because the company works systematically, an unannounced audit can take place without any problems. There is a central action list for certification issues. | The GFSI guidelines are also monitored in order to be able to anticipate changes in quality standards in time. The company is protesting the failure of the auditor because there is knowledge of the standard and the complete certification process. |
Food Safety Compliance: demand relationship management (DRM)
Getting Connected | Networking | Sense and Respond |
Customer questions are answered reactively and product specifications are issued on request, after a year there is no overview of who has been promised what. A customer audit leads to disappointment with the customer, because the agreements made are not known within the company and are not complied with. | There is a company-wide system for customer communication, which records who communicates what. The company demonstrably works according to additional customer requirements and a customer audit leads to extra bonding with the customer. There is a central action list for customer issues. | It is known which themes will become important for customers and proactive anticipation is given. Corporate social responsibility and chain transparency are part of the customer approach, in which there is cooperation on improvement. |
Food Safety Compliance: business performance management (BPM)
Getting Connected | Networking | Sense and Respond |
There are instructions at department level, in case of deviation the department manager is involved. There is an overview of actions at department level, recorded in the minutes of the department meeting. There is no company-wide action list that is centrally managed. | There is a company-wide system for food safety, which determines who carries out what. Work is demonstrably according to the requirements and an internal audit leads to involvement and company-wide improvements that are addressed via the central action list. | There is a holistic approach to food safety, which defines who performs what. The company demonstrably works on identifying and following up on the latest food safety issues and works together with suppliers, customers and industry organizations on transparency and trust within the Global Food Supply Chain. |
Food Safety Compliance: supply relationship management (SRM)
Getting Connected | Networking | Sense and Respond |
Purchasing specifications have been drawn up for suppliers, but there is no overview of agreements. There is no company-wide system for supplier communication, in which it is determined who communicates what. | There is a company-wide system for supplier communication, which records who communicates what. Compliance with supplier agreements is demonstrably monitored and an audit on location at the supplier leads to extra commitment.There is a central action list for supplier issues. | It is known which themes will become important within the supplier relationship and these are proactively anticipated. Corporate social responsibility and chain transparency are part of the supplier approach, where there is cooperation on improvement. |
Food Safety Compliance: legislation management (LM)
Getting Connected | Networking | Sense and Respond |
The quality system is set up in accordance with the legislation, but is not aware of the latest legislation or interpretations. A month before a system audit, every effort is made, an unannounced visit by the Food Safety Authority often leads to a warning or fine report. | The quality system is set up in accordance with the legislation and the latest guidelines. Because the company works systematically, an unannounced audit can take place without any problems. There is a central action list for legislative issues | New legislative processes are also monitored in order to be able to anticipate changes in legislation and enforcement in time. The company is protesting the failure of the Food Safety Authority because it is aware of the legislation, but also of the entire enforcement process. |
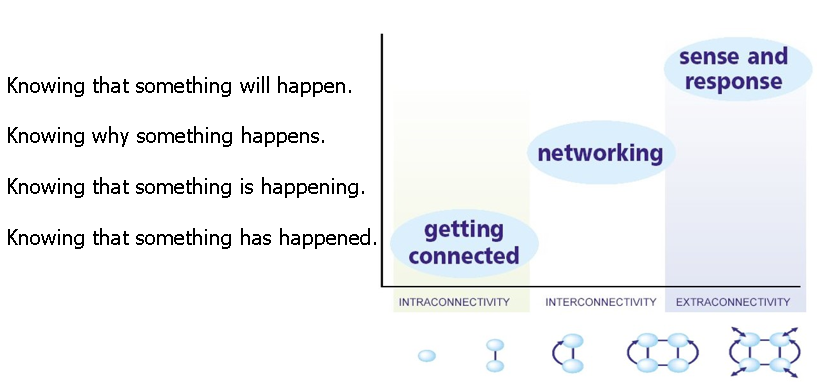
The degree of connectivity of the company says a lot about the learning capability of the company. Food Safety Compliance management focuses on safeguarding risks where the company needs a holistic approach regarding food safety, food defense and food fraud. In addition to the basic requirements for food companies, a company must be organized in such a way that the Hazard Analysis of Critical Control Points (HACCP), Threat Analysis of Critical Control Points (TACCP) and Vulnerability Analysis of Critical Control Points (VACCP) remain up to date. Carrying out a HACCP, TACCP or VACCP study alone is not sufficient.
The company must focus on a holistic approach to business performance, demand and supply relations, legislation and certification, creating a learning organization about Food Safety Compliance. The company knows what will happen so the associated risks can be proactively managed.
Related articles to Food Safety learning application in the organization
Many customers and visitors to this page 'Food Safety learning application in the organization' also viewed the articles and manuals listed below: